前回は、待ち行列理論を生産現場で使うことはほとんどない、という話をしました。複数の工程が連なる実際の生産ラインに適用できる待ち行列モデルはないし、定常状態という条件も現実的ではないし、使いにくいというよりはほとんど使えないのが現実。
ところが、ところがです、、。藤本隆宏教授の著書を読み進めていると、現場ではほとんど使うことのない待ち行列理論が実は、極めて重要な知見ではないか、と。特に、藤本教授が主張する「良い設計の良い流れ」を生産現場で具現化するときにすごく役立つかもしれない、、。
こういうと、藤本教授の著書には「良い設計の良い流れ」と待ち行列理論との関係が、理路整然と説明されているのかというと、そうではなく、まったく逆です。そんな説明はどこにもなし。待ち行列理論への言及はあることはあるんですが、EOQ問題とか安全在庫問題でインプットがどうの、アウトプットがこうの、という的はずれなものだけ。
つまり、藤本教授の著書には生産ラインの基本特性である工程の稼働率と、工程前で滞留する仕掛数(あるいはその待ち時間の長さ)との関係を待ち行列理論で説明しているところはまったくないんです。
藤本教授にお聞きしましたところ、待ち行列理論ではなくて、「流体力学や渋滞学」で説明できるとのこと。念のため、具体的な数理的説明をお願いしましたが、「文系的な説明」しか返ってきませんでした。
「工程前でワークが待つ時間はその工程の稼働率の影響を受ける」という生産ラインの基本特性を記述する待ち行列理論なしに、「設計情報転写論」とトヨタを対象とした「生産システムの進化論」にどのような影響を及ぼしたか、調べてみたいと思います。
1、設計情報転写論
藤本教授の著書の多くに、必ずといっていいぐらい出てくる「設計情報転写論」。生産について次のように説明をしています。
生産とは設計情報の転写(設計情報を媒体すなわち直接材料に移転すること)であり、転写の速度・密度・精度で産業現場の競争力は決まる。
競争力で重要なファクターである生産リードタイムは次の式で与えられると主張します。
生産リードタイム=1/(情報受信スピード×情報受信密度)
この式の中に何か秘策が隠されているのか。いろいろ考えてみましたがわかりません。不可解な式です。で、藤本教授にもお聞きしました。が、納得できる説明はありません。生産の「流れ」の良さを左右する重要な生産リードタイムが設計情報転写論ではどのように定義されるのか、はっきりしません。
なぜでしょう?
生産の「流れ」を設計情報の転写という概念で抽象化するとき、「モノの側面を捨象」した、と藤本教授は説明します。「モノが流れる物理現象」を排除しちゃった。転写受信スピードに気をとられ、工程がビジーで転写できない時間があること、つまり待ち時間があることが意識の中から「スッポリ」と抜けてしまったんでしょうか。銀行の窓口だってATMだって、先客がいれば待たなきゃいけませんよね。
「モノの側面を捨象」することで、販売やサービス業も取り込み「広義のものづくり」へと適用範囲を広げることはできました。が、肝心の生産ラインでは使えなくなった、ということにはお気づきになっていないようです。
「工程の稼働率とその前でワークが待つ時間の関係」を知っていれば、「モノの側面を捨象」することはなかったのではないか、と思うわけです。
2、生産システムの進化論
2.1 生産ラインの基本特性を無視すると、トヨタとは、
トヨタを分析の対象とした「生産システムの進化論」(藤本隆宏著、1997年)での結論は下記のようになっています。
トヨタとは、
情報システムの構造的複雑さにより他社の模倣を妨げ、
組織成員が共有する健全な「心構え」に支えられた、
事後合理的能力構築能力を創発し続けるシステムである。
ー(筆者要約)ー
「トヨタ生産方式を再現できた企業は皆無」(ハーバード・ビジネス・レビュー、1999年)と同様な見解は他でもよく聞き、共通認識となっています。「情報システムが複雑」なことがその理由だ、とする根拠はどこにあるのでしょうか。合理的な説明はどこにもありません。そして「心構え」という精神論を持ち出しますが、「豊田佐吉や豊田喜一郎の思想的影響を挙げるのが、組織文化論の一つの定石である」(367p)の対論としては、説得性に欠け、お粗末すぎます。事前にではなく、後になって合理的だと分かるような事後合理性で、つまり「怪我の功名」の連鎖でトヨタは進化してきた、と主張します。トヨタが「怪我の功名」の連鎖でェ? これが本当なら、こちらの方が「他社の模倣を妨げる」理由になるのではないでしょうか。「怪我の功名」って、まねできませんよね、、。
「生産システムの進化論」には、生産ラインの基本特性である「工程の稼働率とその前でワークが待つ時間の関係」を記述する待ち行列理論への言及はまったくありません。従って、前記の結論は、生産ラインの基本特性をまったく考慮せずに導き出されたものである、と判断されます。
2.2 大野耐一著「トヨタ生産方式」では、
では、それを考慮していたら、どのようなトヨタ進化論になるのか。「トヨタ創業者の思想」をトヨタ生産方式へと具現化した大野耐一が著した「トヨタ生産方式」、1978年 が手がかりになるのではないかと思います。
書には、待ち行列理論への言及はまったくありませんが、Just In Timeの実現を目指しながらの思考実験、生産現場の問題の捉え方や解決策、経験則を織り交ぜた試行錯誤などを通して、一歩一歩トヨタ生産方式が形作られていく様子を感じ取ることができます。生産ラインの基本特性という切り口で、トヨタ生産方式の進化論的ナラティブを探してみたいと思います。
2.3 生産ラインの基本特性とトヨタ生産方式
トヨタ生産方式といえば、お馴染みのJust In Time。生産ラインの視線でみれば、必要なときに、必要なものだけが、そのつどJust In Timeで到着する。トヨタの創業当初に豊田喜一郎がいいはじめたJust In Time は、いま尚、トヨタ生産方式の基盤であり続けています。
生産ラインの基本特性およびそのメカニズムを論理的に記述する待ち行列理論という括りでトヨタ生産方式の特徴を調べてみたいと思います。
まず、生産ラインの基本特性の一つである工程前で待つワークの平均待ち時間の近似式を示します。
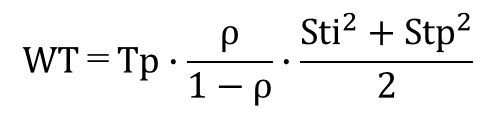
到着時間間隔 ― 平均;Ti、変動係数;Sti
処理時間 ― 平均;Tp、変動係数;Stp
稼働率 ― ρ=Tp/Ti
平均待ち時間 ― WT
この式の背後にあるモノ(ワーク)の流れるルールは、水は高きより低きに流れるように、上流工程から下流工程に常に流れるプッシュ型を条件にしています。ワークが流れ着いたとき工程がビジーであれば処理が終了するまで待つことになります。
図1に平均処理時間に対する平均待ち時間(WT/Tp)が稼働率(ρ)や到着時間間隔(Ti、Sti)、処理時間(Tp、Stp)でどのように変わるかの一例を示します。
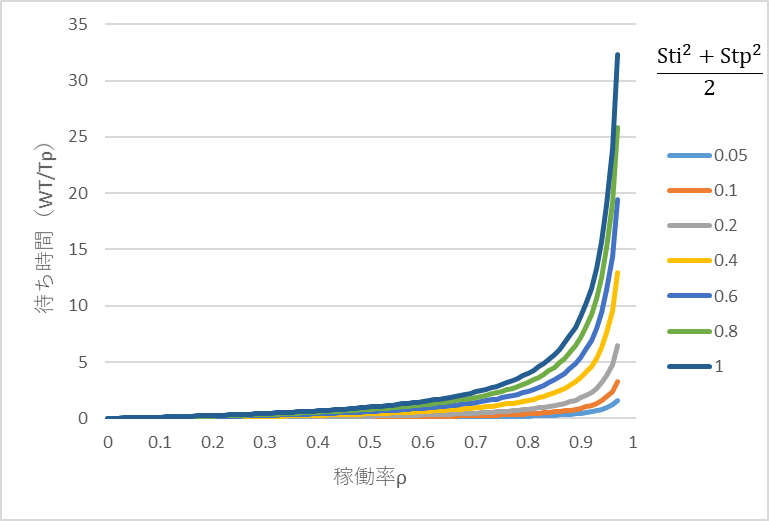
図1 待ち時間の特性
一般的には、できるだけ高い稼働率(ρ)を目指しますが、トヨタ生産方式でもρを高く維持することを重視します。ρを高く維持しながらも、平均待ち時間(WT)を短くするためには、工程に投入される時間間隔のバラツキ(Sti)や工程の処理時間のバラツキ(Stp)を小さくする必要があります。StiやStpを小さくする方法として次のようなテクニックがあります。
平準化生産、ラインバランスをとる、標準(時間、作業、動作、、)の徹底、サイクルタイムでの同期生産、ムダの排除、、
また、バラツキを吸収するテクニックもあります。
多能工による多工程持ち、バトンタッチゾーンの設定、自律完結工程、標準手持ち、セグメント間バッファー、、
待ち時間が長く(滞留仕掛が多く)なると、そのバラツキも大きくなりラインの管理が不安定になります。それを防ぐ仕組がトヨタ生産方式特有の後工程引き取り「かんばん方式」です。
プッシュ型の一般の生産ラインでは、稼働率を気にするあまり、投入過多になりやすく、工程間に仕掛が溜まりやすくなります。図1を見てわかるように、急激に待ち時間が長くなる(待ち時間の跳ね上りが起きる)と進捗管理などが煩雑になり不安定になります。「かんばん方式」は必要な分しか引き取らないプル型なので、条件設定により過剰投入を防ぐことができるようになります。図1で言えば、急激に待ち時間が跳ね上がる領域に入らないようにするということです。
管理が不安定な領域に入るのを防ぐ仕組みとして、次のようなものがあります。
ムダ(特に作りすぎのムダ)の排除、自働化、アンドン、作業者のラインストップ権限、ポカヨケ、かんばん方式、平準化生産、、
2.4 トヨタ生産方式の基盤
生産ラインの基本特性からみたトヨタ生産方式の基盤として、以下の三つを挙げておきます。
- Just In Time と自働化
「Just In Time」と「自働化」は、要求されるQCDを実現する生産ライン構築の基本概念であり、いま尚、進化するトヨタ生産方式を支える中核的思想である。
- 流れ生産ラインの基本要素
自動車生産を見すえた流れ生産ラインの能力として、稼働率と生産リードタイムが重要である。それを決める要素は、工程の処理時間、ワークの到着時間間隔および、それぞれの平均とバラツキの4項目である。
- プル型の「かんばん方式」で「流れ」を逆転、待ち時間の跳ね上り現象を抑制
一般のプッシュ型生産では稼働率に対する待ち時間の跳ね上り現象が必然的に発生し、滞留在庫の増加、生産リードタイムの長期化などの主な要因となっている。トヨタ生産方式では、一般的なプッシュ型の「流れ」を逆転させて、必要な分だけを引き取るプル型の「かんばん方式」を導入。さらに平準化生産を取り入れるなどして、待ち時間の跳ね上り現象を抑制している。
一般的な生産ラインはプッシュ型ですが、トヨタ生産方式ではプル型の後工程引き取り「かんばん方式」で高稼働率領域での待ち時間の跳ね上りを抑制しているのが特徴です。トヨタの場合でも実際の生産ラインは、プッシュ型とプル型の混合です。到着時間間隔・処理時間のバラツキ縮小・吸収するための創意工夫を継続し、高い稼働率を維持しながらも、待ち時間の発生を抑制し、Just In Timeを実現しているのがトヨタ生産方式の特徴であるということができるのではないでしょうか。
その他に、創業者トップの強力かつ継続的な支持さらに生産調査部のサポートなど全社をカバーする組織的態勢ができてきたなど、生産ラインの基本特性に関すること以外にもトヨタの進化に大きな影響を及ぼした要因は多々あると思いますが、この辺りについては、今後、調べてみたいと思います。
3、とりあえず、まとめ
藤本教授は、トヨタを対象とした「生産システムの進化論」で、独自の設計情報転写論や事後合理的創発論、進化論などをベースに分析しています。分析に用いた理論や枠組みの中には、生産システムが持つ基本特性および、それを記述する待ち行列理論は考慮されておりません。
一方、「トヨタ生産方式」を「待ち行列理論で記述できる生産ラインの基本特性」という枠組みでみると、「トヨタ生産方式の基本概念、それを具体化した方法」と「生産ラインの基本特性」との間に多くの共通項が確認されます。「トヨタ生産方式」が科学的、工学的、物理的理論で裏打ちされていることが、トヨタの発展と独走を支えている重要なファクターであるという巷の最大公約数的見解とほぼ一致します。
生産現場で使うことはほとんどないし、あまり重要な理論ではないと思われた待ち行列理論ですが、実は、生産システムの基本特性を正しく理解するためには、重要な理論である、という思いを強くしております。
先に挙げた藤本教授の結論を再掲します。
トヨタとは、
情報システムの構造的複雑さにより他社の模倣を妨げ、
組織成員が共有する健全な「心構え」に支えられた、
事後合理的能力構築能力を創発し続けるシステムである。
技術・生産管理、トヨタ生産方式等の生産管理方式を専門とする元東大教授が導き出した結論です。